1. Introduction
In this article, we will learn the effect of adding anti-freeze agents (Glycol) to chilled water, in an HVAC chilled water system.
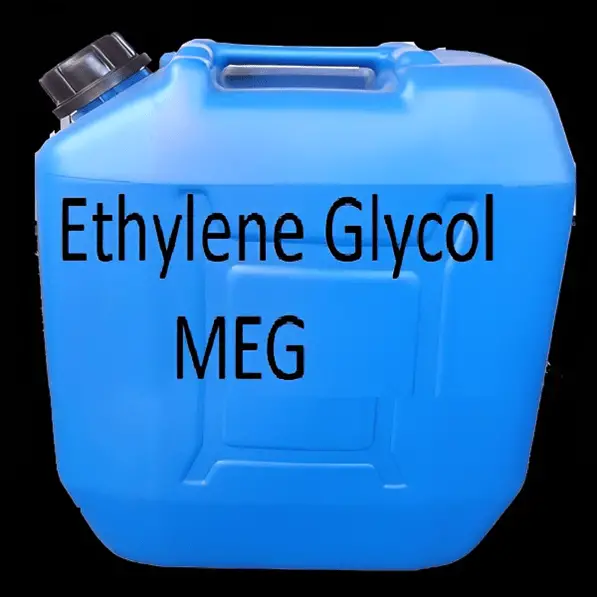
For applications with larger cooling capacities, a chilled water system is used to remove heat from the space, room, or other source. The extracted heat is then transferred to the cooling mediums (i.e., ambient air in an air-cooled chiller system or water in a water-cooled chiller system).
The major components of a chilled water system are as below:
1) Chiller (Air-cooled, water-cooled), dry cooler
2) Chilled water pumps
3) AHUs/FCUs
4) Chilled water pipework (including fittings, valves, strainers, etc.)
5) Expansion tanks
6) Pressurization unit
7) Air separator
8) Chemical dosing system
9) Instruments and controls
2. Freeze Prevention
Normally pure water is used as a cooling medium in the chilled water system.
The freezing temperature of pure water is 0 OC (at a standard atmospheric pressure of 1 atm).
For projects located in cold countries (e.g., European countries, the UK, Russia, the US, and Canada, etc.), during extreme winter conditions, chilled water in the fresh air AHU, dry cooler cooling coil, and externally routed chilled water pipework will be exposed to sub-zero ambient air temperatures.
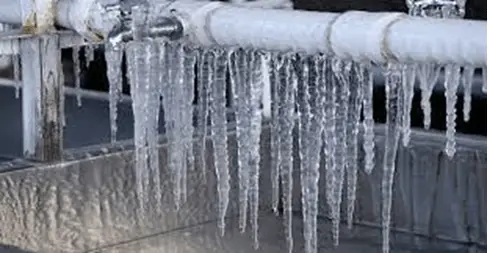
We should note a point that by adding insulation to the chilled water pipework the heater transfer flow rate between the subzero ambient air to the chilled water inside the piping system can be reduced, however the insulation cannot completely stop the heat transfer. If the surrounding air temperature remains low enough for an extended period, insulation cannot prevent freezing of still water or of water flowing at a rate insufficient for the available heat content to offset heat loss.
Water freezing affects the functionality of the system. Sometimes freezing of water may lead to rupture of the water pipework, and its joints. This is due to the reason that, when water is freezing, it expands and its volume increases drastically. Increase in water volume creates additional stress to the pipe system and it may lead to rupture.
So, to avoid freezing of water and subsequent rupture of the pipework & HVAC system failure, additives like glycol should be added to the water.
3. Impact of glycol addition
Adding glycol (commonly ethylene glycol or propylene glycol) alters the physical and chemical properties of the pure water.
Below properties value of water decreases:
- Freezing point temperature
- Specific heat capacity (Cp)
- Thermal conductivity (k)
Below properties value of water increases:
- Boiling point of water
- Density
- Viscosity
- Prandtl number
Based on the extreme winter ambient temperature persists in the project location, the amount of glycol (% by volume or % by mass) should be added to the water so that the mixed solution (Pure water + glycol) freezing temperature is lower than the extreme winter temperature.
Addition of glycol to the pure water will have the following negative impact to the design, and performance of the overall HVAC system.
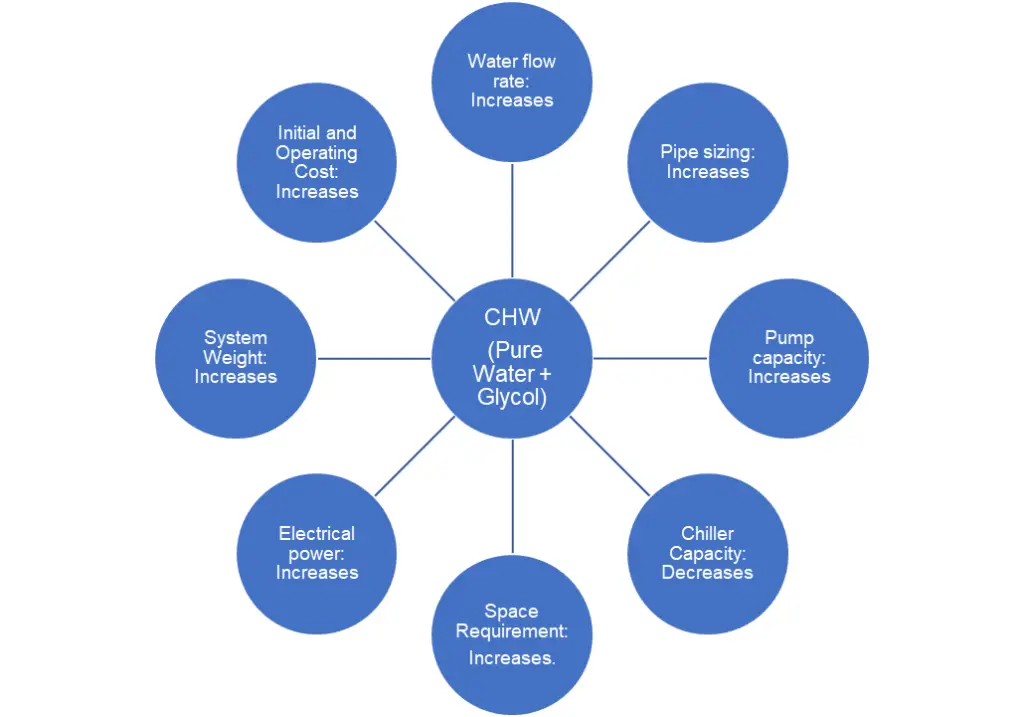
4. Case Study
In the following sections we will learn the impact due to addition of glycol with sample calculation.
Consider the following design values.
- Total cooling capacity (Q): 100 TR (=351.7 kW)
- Water cooled type chiller
- CHW in/out temperature: 12 OC/6 OC
- Project location : Berlin Dahlem, Germany
- Return period : 50 Years
4.1 Selection of ambient air temperature
Refer below the extract from the “ASHRAE Fundamental, Chapter Physical Properties of Secondary Coolants (Brines)”
“If the application requires that the fluid remain entirely liquid, use a concentration with a freezing point 3 K below the lowest expected temperature. Avoid excessive glycol concentration because it increases initial cost and adversely affects the fluid’s physical properties.”
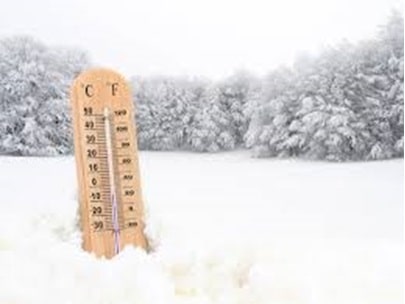
So firstly, the lowest expected temperature should be identified from the weather data (metocean data) of the project location.
The important points to note that, taking the extreme winter temperature from ASHRAE weather data will not give the correct extreme temperature value to decide glycol percentage.
For example, consider the below table, taken from ASHRAE weather data.
As per this table extreme ambient air temperature of minus 12 OC (based on 99.6%) has been specified.
Note the important point that, this condition can be used for sizing ONLY the heating equipment and not for deciding the extreme ambient air temperature and associated percentage of glycol to avoid freezing. The reason is that these table data are based on the average past data and also the 99.6% will not reflect the actual extreme air temperature.
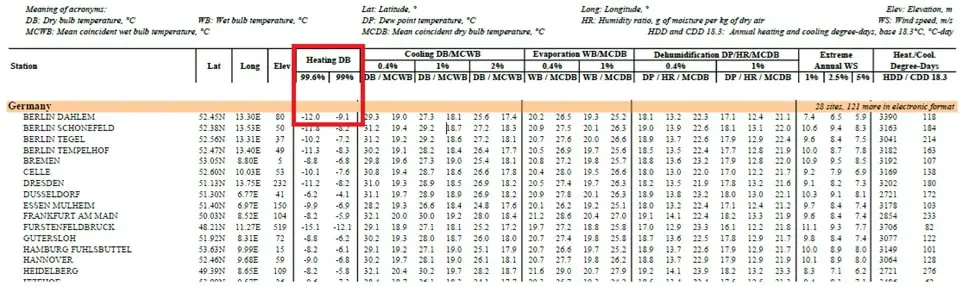
So, we need to get the project specific metocean document. Also, we need to understand the project life cycle and the requested design return period specified by the client.
Below table is not for the GERMANY, it is for some other hot country. For explanation purpose I took this table. If the client specification says to design the system for 50 years “Return period” then 18.7 OC should be taken as an expected extreme minimum air temperature.
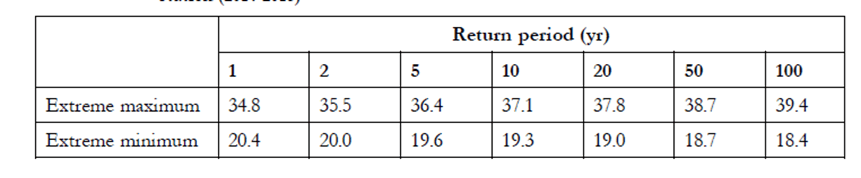
Then applying 3 K safety margin set by the ASHRAE, the temperature of 15.7 OC (18.7 – 3) should be considered for selecting the glycol percentage.
The common mistake what we do is by selecting the AVERAGED minimum extreme air temperature (refer to below table).
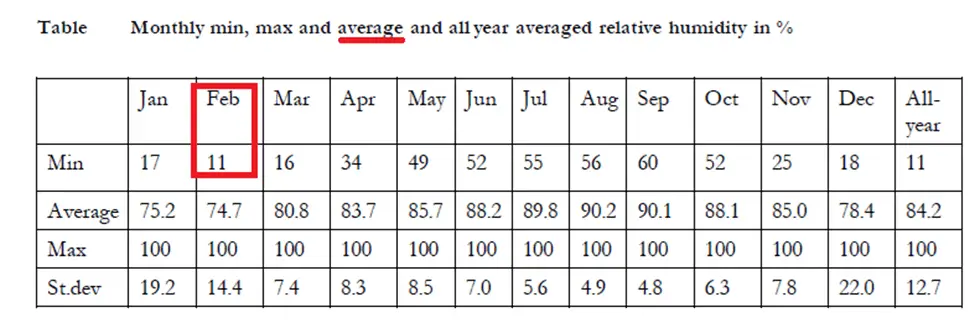
So as explained above the “extreme air temperature” and “Return Period” concept should be applied.
I do not have the metocean document for “Berlin Dahlem, Germany”, for explanation purpose I will consider minus 13 OC as the expected “extreme minimum air temperature” for the “return period” of 50 years.
Conclusion: So the extreme air temperature of minus 16 OC (=-13 – 3) should be used for deciding the glycol concentration.
4.2 Selection of glycol percentage
Glycol can be ethylene or propylene type. For the explanation of this blog I will consider ethylene glycol and properties will be taken from “Tyfocor brand glycol”.
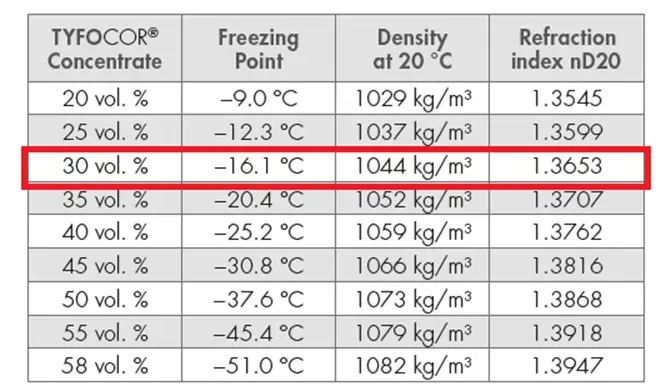
4.3 Property comparison
The thermal properties of pure water and water + glycol are given below:
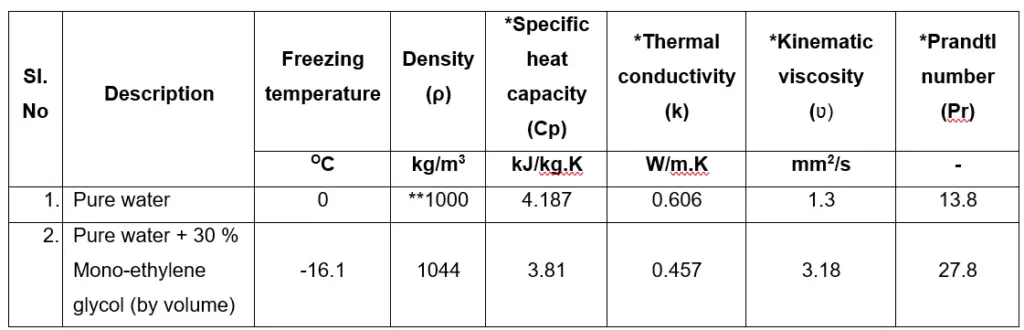
Density
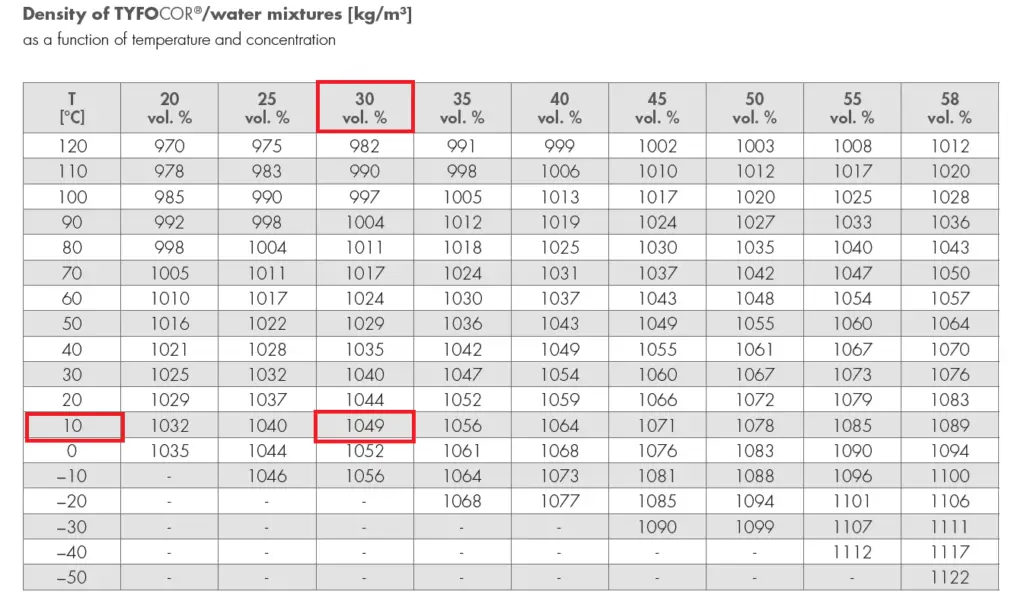
Specific heat capacity
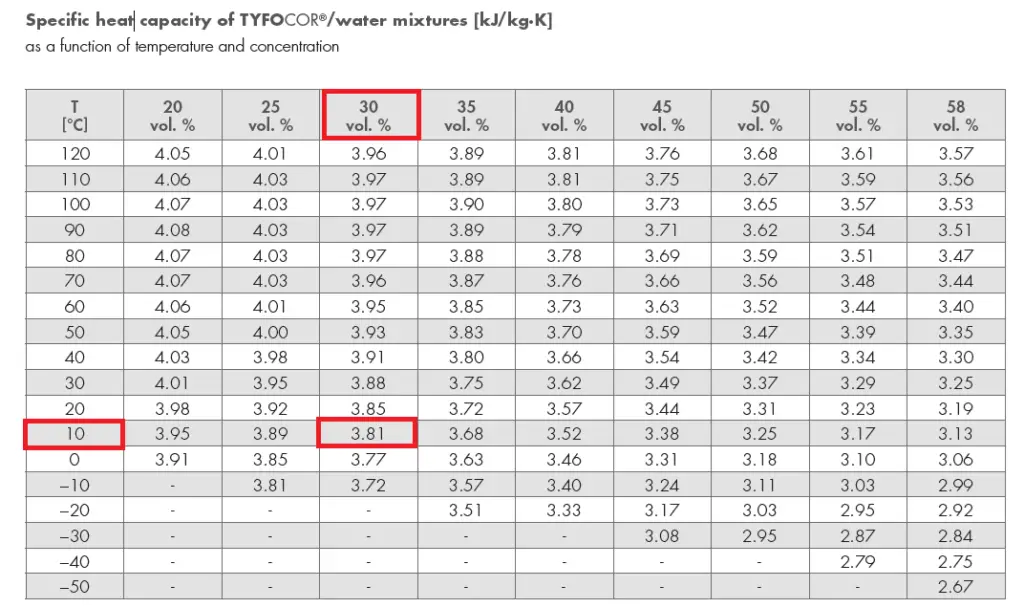
Thermal conductivity
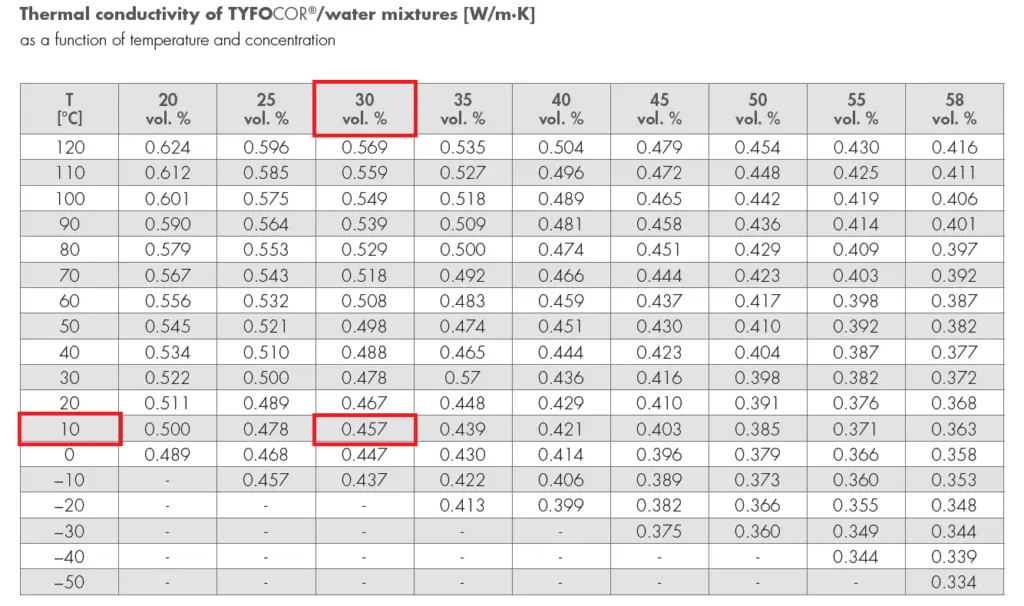
Prandtl Number (Pr)
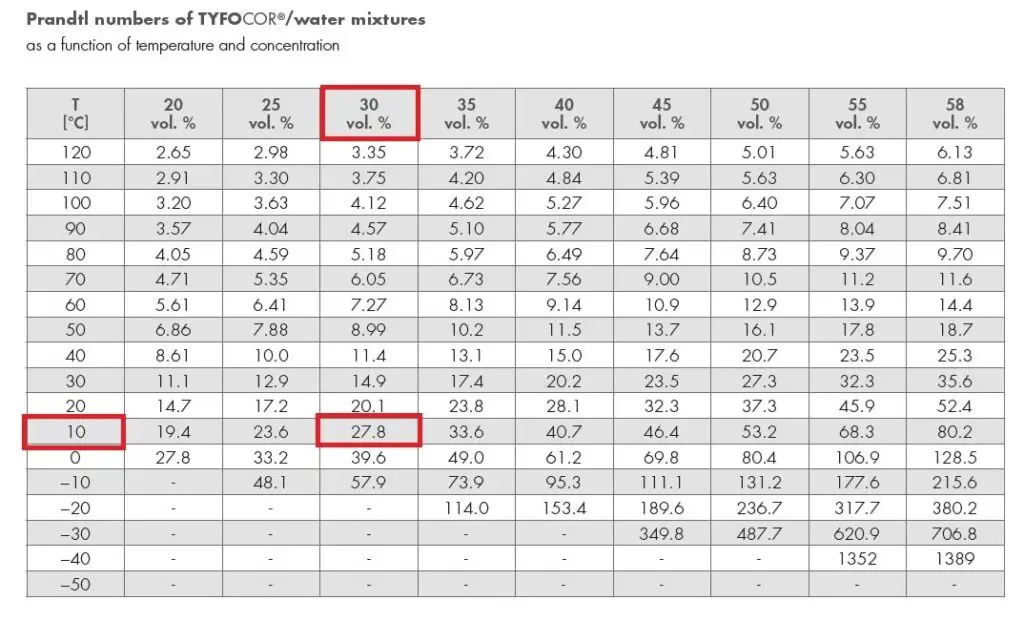
4.4 Chilled water flow rate calculation
Q (kW) = Mass flow rate (kg/s) x Specific heat capacity (kJ/kg.K) x ΔTCHW (OC)
Case 1 : Pure water (Density = 1000 kg/m3)
351.7= Mass flow rate (kg/s) x 4.187 x 6
Mass flow rate = 351.7/ (4.187 x 6)
=14 kg/s
= 14 L/s
Case 2 : Pure water + 30 % glycol (Density = 1049 kg/m3)
100×3.517= Mass flow rate (kg/s) x 3.81 x 6
Mass flow rate = 351.7/ (3.81 x 6)
= 15.39 kg/s
= 14.67 L/s
% Increase in volumetric flow rate requirement = ((14.67/14)-1)x100
= 4.79 %
Conclusion: To cater the same total cooling load (100 TR), about 5% of more volumetric chilled water flow rate is required in case pure water is mixed with 30% glycol by volume
4.5 Pipe Sizing
The frictional drop is hf = fxLxV2/2gD
Reynold’s number (Re) = UD/ʋ
Colebrook’s equation
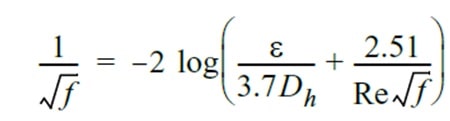
As the volumetric flow rate with 30% glycol is about 5% is more than pure water, and due to the higher viscosity of water + 30% glycol mixture, for a given pipe size, the Reynold’s number (Inertial force/viscous) decrease and consequently the frictional loss increases.
Note that the standard frictional loss chart or software tool cannot be used, as the properties (Viscosity, density) values are different from pure water.
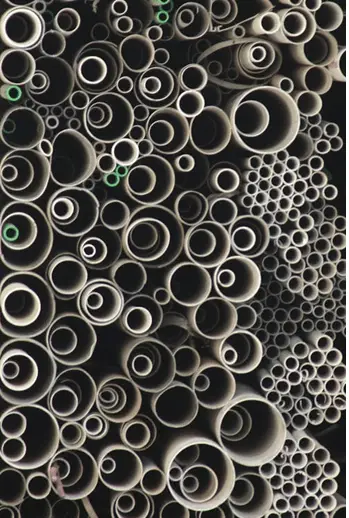
Note that as the viscosity and density value increase, the pressure drop inside the equipment also increases.
Conclusion: So pipe sizes should be increased, if the same pressure drop of pure water to be achieved. Due to the increase in pressure drop inside the equipment, the overall pressure drop in the piping system (including equipment), increases.
4.6 Pump capacity
Pump power = ΔP (Pa) x flow rate (m3/s)/( Efficiency of pump x Efficiency motor)
As the Pressure drop, and volumetric flow rate is higher in the chilled water system with glycol.
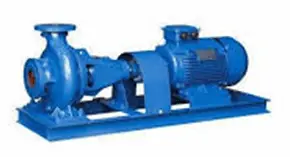
Conclusion: Pump capacity (Head, flow) and the required electrical power increases in the chilled water system with glycol in comparison with pure water.
4.7 Chiller capacity:
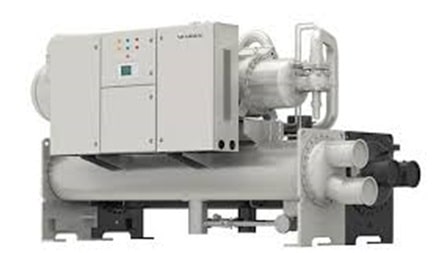
Due to the addition of glycol to the pure water, the thermal conductivity of mixed water decreases.
Nusselt’s Number (Nu)=0.023 x Re0.8 Prn
Where,
n= 0.3 for cooling and 0.4 for heating. Water is assumed to flow through the tube in the evaporator
h= Nu x k /D
Consider tube diameter as 25mm (=0.025m) and flow velocity as 2 m/s.
Case -1 (Pure water)
Convective heat transfer co-efficient (h) = 0.023 x (UD/ʋ)0.8x Pr0.3
= 0.023 x (2×0.025/1.3×10-6)0.8x (13.8)0.3
= 0.023 x 4656 x 2.2
= 235.6 W/m2.K
Case -2 (Pure water + 30% glycol by volume)
Convective heat transfer co-efficient (h) = 0.023 x (UD/ʋ)0.8x Pr0.3
= 0.023 x (2×0.025/3.18×10-6)0.8 x (27.8)0.3
= 0.023 x 2276 x 2.69
= 140.82.6 W/m2.K
Conclusion: As the convective heat transfer co-efficient (h) on water side decreases with addition of glycol, the heat transfer rate decreases, and it degrade the chiller capacity. So due to glycol effect, the chiller model may be selected one size up.
This means that to produce the same cooling capacity, the chilled water system with glycol mixture require more electrical power.
4.8 Electrical Power Requirement
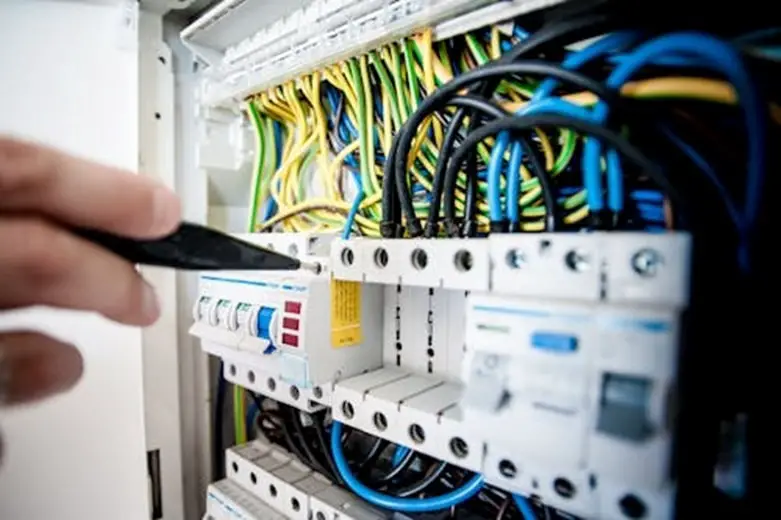
From the above point, it is clear that, to produce the same cooling capacity (TR) the electrical power required in system with glycol is higher (due to the chiller de rating and additional power requirement of chilled water pumps).
4.9 System Weight
The weight of chilled water system with glycol is higher than the pure water system. This is due to the following reasons:
- Bigger pipe size and associated internal water content, support weight
- Bigger chilled water pump capacity. Indirect weight increase due to increase in electrical power supply system (Cable, trays, support) also should be also considered.
- Bigger chiller size. Indirect weight increase due to increase in electrical power supply system (Cable, trays, support) also should be also considered.
4.10 Initial and Operating Cost
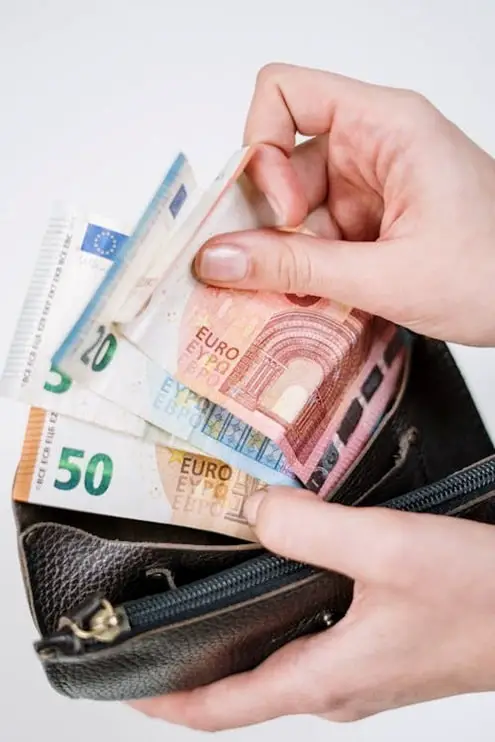
Initial cost is higher in the system with glycol due to bigger pipe sizes, higher chiller and pump capacities.
5. CONCLUSION
Adding glycol to chilled water system has several adverse impacts, including increased pipe sizing, bigger equipment sizes, higher electrical power consumption, increased overall system weight, increased space requirement, increased initial and operating cost, sustainable environment. Additionally it poses challenges for maintaining a sustainable environment (for countries the electrical power is obtained by burning the fossil fuel)
The primary benefit of adding glycol is its ability to lower the freezing point of the water, which protects the HVAC chilled water system from freezing, rupture, and potential HVAC system shutdowns and associated main plant operation shut-down.
To maximize efficiency and minimize drawbacks, it is essential to carefully calculate and add the correct percentage of glycol to the system, ensuring optimal performance and system protection.
6. REFERENCES:
- ASHRAE Handbook – Fundamental, Chapter “Physical Properties of Secondary Coolants (Brines)”
- Tyfocor brand glycol catalogue
- Steam Table
7. ABBREVIATIONS:
AHU | Air Handling Unit |
CHW | Chilled Water |
FCU | Fan Coil Unit |
HAP | Hourly Analysis Program |
HVAC | Heating, Ventilation, and Air Conditioning |
UK | United Kingdom |
USA | United States of America |
TR | Ton of Refrigeration |